Gravity Die Casting
- Ayushi Singh
- Aug 13, 2018
- 3 min read
With sand casting the mold is split up after every casting operation, but with the procedure referred to as gravity die casting, the mold also known as a 'die' is made of metallic, and can be utilized a large number of times. Which means that the die is a lot more expensive to create, than an expendable 'one use just' mold.
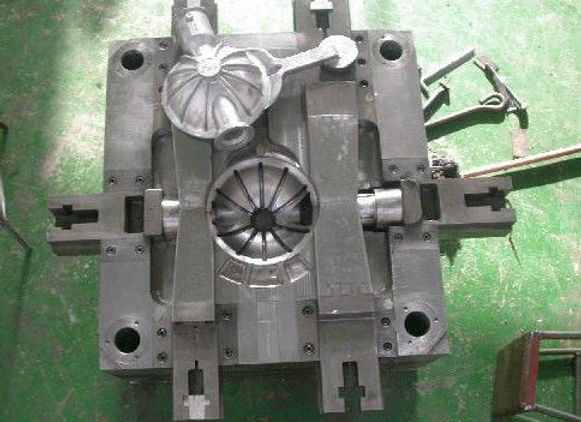
An intermediate method employs semi permanent molds, which are constructed of gypsum fireclay or plaster, which can be useful for a limited amount of castings repeatedly. With gravity die casting, probably the most used components for die-making are usually cast iron widely, steel, and high temperature resisting alloys of iron.Visit this website for more info about Air Plasma Spray Coating and Thermal Spray Coating here.
For a few specific purposes other components are used to produce the dies, and these range from, aluminum. graphite or copper. A metal die can produce soft castings with a clear surface, and an extremely high dimensional precision. These castings require hardly any or no last machining or various other finishing treatment. The assistance life of metal dies may differ in terms of the true number of castings it could produce, and this depends upon certain factors like the casting materials, the thermal metal shock resistance of the die materials, the temperature of which it really is poured, and the casting technique employed.
Many different details have to be taken into account when making the pattern that the die is manufactured. For example the pouring-gate program and risers have to be considered so the wall space of mold allow a quenching motion upon the molten metal so that it van solidify quicker than in sand casting. Also the die should be provided with stations at the joints and surroundings vent holes to permit air from the sizzling metal to flee from the inside of the die.

The die must be constructed so that it shall not really restrict the shrinkage occurring, when the metal cools. Shrinkage can existing difficulties when making the cores which type the casting. The cores are made from steel or exclusive alloys usually, and compressible sand or shell cores are employed sometimes.
To avoid the casting metal from sticking with the die, the die could be given an internal covering of chalk, clay, or bone ash with drinking water glass as a binder. This mix can be put on the die by spraying, immersion or brushing.Get to know more about Gravity Die Casting here.
With simple castings the molten metal might be poured in at the very top. It should be made to allow the molten metal to flow rapidly without turbulence into all elements of the die. For metals with low melting factors the die will be heated to avoid premature solidification sometimes, and for metals with a higher melting point, the die may need to be cooled after every casting operation artificially.
Gradually moving or tilting the die while casting may reduce turbulence and enable the metal to flow even more smoothly, when large castings are increasingly being produced particularly.
For shaped castings awkwardly, a vacuum might be applied to assist the filling of the die. Slush casting, is really a technique used for making ornamental or hollow castings: the molten metal is poured in to the die, and when a good shell of sufficient thickness has produced, the remaining liquid will be poured out.
Although die castings are cheaper than sand castings, the die tooling is more costly, and an optimum amount of castings have to be produced to help make the process cost effective.
Commenti